Ceramic Copper
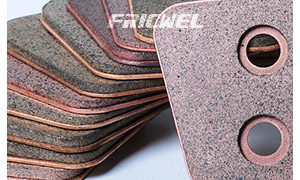
Copper clutch buttons, made with advanced ceramic friction materials, are designed to meet diverse market needs through two distinct formulations.
1.Standard Formula features a classic copper finish with stable friction and wear performance, providing excellent resistance to fading and making it a reliable choice for various applications.
2.Low-Wear Formula, on the other hand, offers an extended service life with reduced wear rates, catering to high-performance requirements, especially in the US and European markets.
In addition to these options, we offer customized formulations tailored to specific customer needs, ensuring optimal performance and reliability for unique applications.
Ceramic Iron
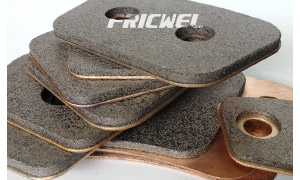
Ceramic iron formula is engineered to align with the material composition standards originally developed for the European market. Currently, it is primarily supplied to our OEM customers and distributed to aftermarket sectors in the United States and South America.
These clutch buttons feature exceptional high-temperature resistance, surpassing the performance of standard copper buttons. With an operating temperature exceeding 600°C and excellent fade resistance at 350°C, they deliver superior durability and reliability under extreme conditions.
Thanks to its cost-efficiency and robust performance, this product has gained significant popularity in recent years, meeting the evolving demands of global markets.
Paper Base
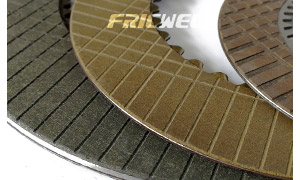
Paper friction material is a key product in our portfolio, offering excellent performance at a relatively low cost. Compared to copper clutch ring facings, the cost of paper friction material can be reduced by 30% or more, making it a highly economical choice.
This material is composed of premium-quality paper, aramid fiber, and glass fiber, providing exceptional wear resistance and stable friction performance. Its reliable properties have made it a popular option among our customers.
Extensive testing confirms the paper formula’s outstanding wear and friction characteristics. It is primarily used in wet clutches for excavators and other heavy-duty machinery, delivering consistent and reliable performance under demanding conditions.
Graphite Carbon
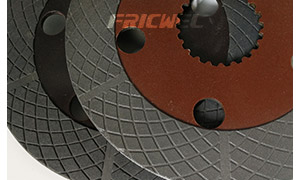
The development of graphite carbon friction products is based on the same design principles as paper friction materials, leveraging cost-efficient raw materials to deliver high performance. Graphite, known for its excellent wear resistance and affordability, serves as a key component in these products, making it indispensable in friction material applications.
Graphite carbon friction products are composed primarily of carbon-based materials, silicon, and other carefully selected friction-enhancing elements. These formulations closely match the performance of paper materials, providing stable friction and wear properties. As a versatile and cost-effective solution, graphite carbon friction products are well-suited for a wide range of applications, meeting the diverse needs of the modern market.
Organic Woven Resin
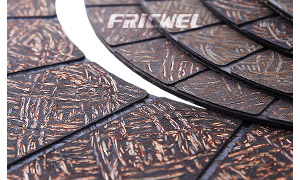
Our production lineup includes a wide range of high-performance friction materials such as Aramid Fiber, High Copper, Compounded Yarn, Covering Yarn, Strong Twisting Fiber, and Glass Fiber. These materials are engineered to meet the specific demands of various applications and markets.
More than 95% of the clutch facings we produce utilize non-asbestos materials, reflecting our commitment to safety and environmental standards.
Market Distribution:
High Copper, Aramid Fiber, and Covering Yarn friction materials are primarily supplied to the European market.
Strong Twisting Fiber in black quality is widely used across North and South America, including for Akebono applications.
Glass Fiber and asbestos-based materials are mainly distributed in Southeast Asia.
Our diverse product range ensures tailored solutions for customers worldwide, meeting stringent quality and performance requirements.
Rubber Base
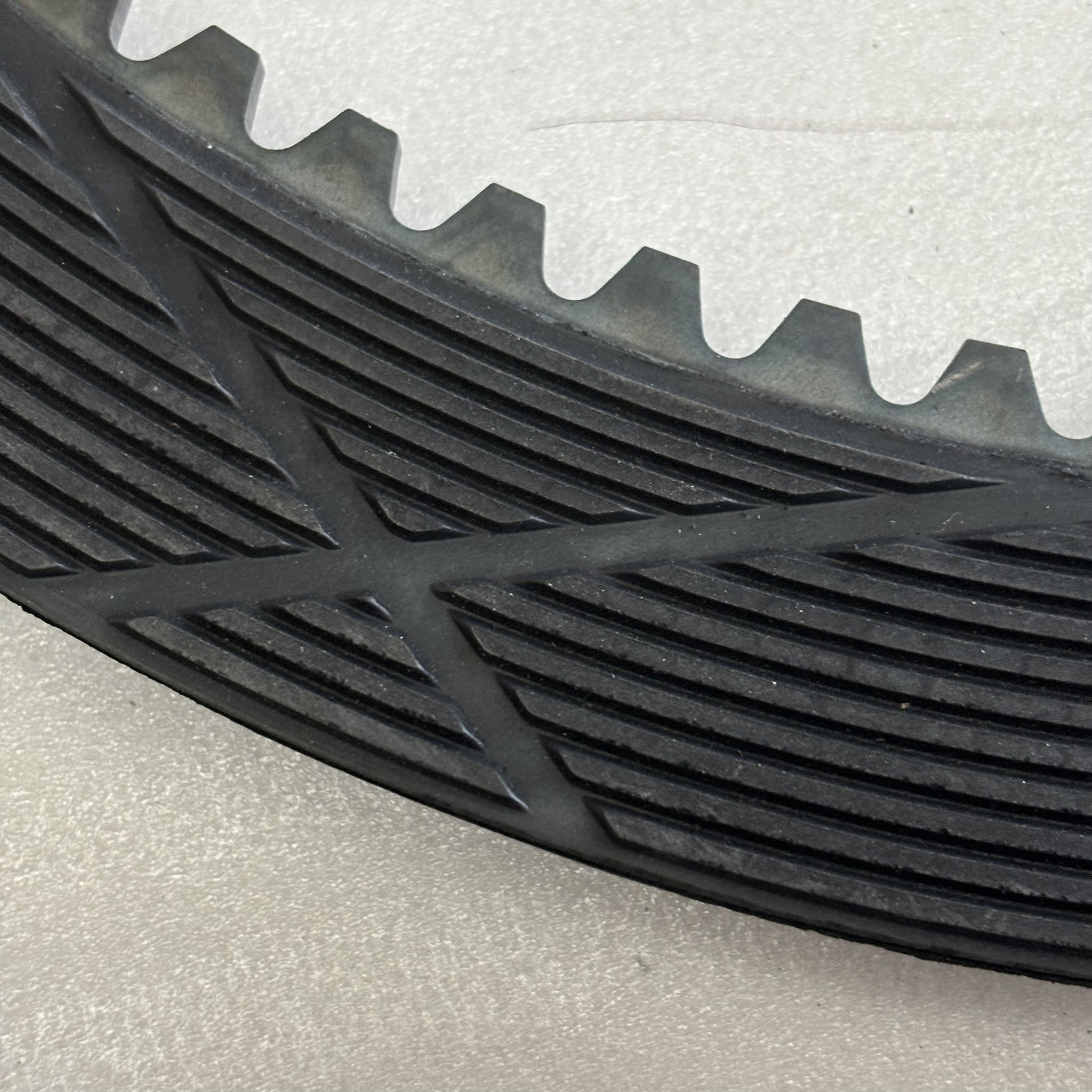
Our newly developed rubber-based friction product was created to meet the specific demands of select customers. With its high elasticity, high modulus, and low hardness, it offers exceptional adaptability to multi-directional deformation, making it suitable for unique working conditions. After multiple tests and adjustments, the product has been successfully introduced, receiving strong interest from several clients.
This innovative material excels in applications requiring cushioning, vibration damping, and stable friction performance. We will provide more detailed information on this product soon—stay tuned for updates on our website.